Verchromte Stahlrohrewerden durch Galvanisieren mit einer Metallschicht auf der Oberfläche des Stahlrohrmetalls beschichtet.Der wichtigste Zweck verchromter Stahlrohre ist der Schutz.Verchromte Stahlrohre weisen eine gute chemische Stabilität auf und reagieren nicht mit Alkali, Sulfiden, Salpetersäure und den meisten organischen Säuren.Verchromte Stahlrohre können sich in Salzsäure (z. B. Salzsäure) und heißer Schwefelsäure auflösen.Zweitens weist die Verchromung eine gute Hitzebeständigkeit auf und verchromte Stahlrohre oxidieren und verfärben sich erst bei Temperaturen über 500 Grad Celsius.Darüber hinaus ist sein Reibungskoeffizient, insbesondere der Trockenreibungskoeffizient, der niedrigste aller Metalle, und verchromte Stahlrohre weisen eine ausgezeichnete Verschleißfestigkeit auf.Im sichtbaren Lichtbereich liegt das Reflexionsvermögen von Chrom bei etwa 65 % und liegt zwischen Silber (88 %) und Nickel (55 %).Chrom verändert seine Farbe nicht und verchromte Stahlrohre können bei Verwendung ihre Reflexionsfähigkeit über einen langen Zeitraum beibehalten, was besser ist als bei Silber und Nickel.Es gibt drei Arten von Verchromungsprozessen.
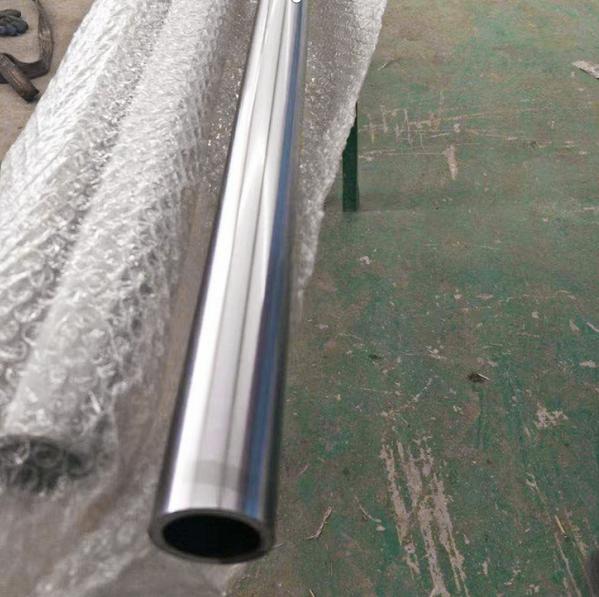
1. Schutz – dekorative Verchromung Schutz – dekorative Verchromung, allgemein bekannt als dekoratives Chrom, hat eine dünne und helle Beschichtung, die normalerweise als äußere Schicht einer mehrschichtigen Galvanisierung verwendet wird.Um Schutzzwecke zu erreichen, muss zunächst eine ausreichend dicke Zwischenschicht auf einem Zink- oder Stahlsubstrat plattiert werden, und dann muss darauf eine helle Zwischenschicht von 0,25–0,5 μ plattiert werden. Dünne Chromschicht von m.Zu den häufig verwendeten Verfahren gehören Cu/Ni/Cr, Ni/Cu/Ni/Cr, Cu Sn/Cr usw. Nach dem Polieren der Oberfläche des Produkts durch dekorative Verchromung kann ein silberblauer Spiegelglanz erzielt werden.Verändert die Farbe nicht nach längerer Einwirkung der Atmosphäre.Diese Art von Beschichtung wird häufig zum Schutz und zur Dekoration von Bauteilen wie Autos, Fahrrädern, Nähmaschinen, Uhren, Instrumenten und Alltagsgegenständen verwendet.Die polierte dekorative Chromschicht hat ein hohes Lichtreflexionsvermögen und kann als Reflektor verwendet werden.Das Plattieren von Mikroporen oder Mikrorissen mit Chrom auf mehrschichtigem Nickel ist eine wichtige Möglichkeit, die Gesamtdicke der Beschichtung zu reduzieren und ein dekoratives System mit hohem Korrosionsschutz zu erhalten.Es ist auch die Entwicklungsrichtung moderner Galvanikverfahren.
2. Die Hartverchromung (verschleißfeste Verchromung) weist eine extrem hohe Härte und Verschleißfestigkeit auf, wodurch die Lebensdauer von Werkstücken wie Schneid- und Ziehwerkzeugen, Press- und Gussformen aus verschiedenen Materialien, Lagern, Wellen, Lehren und Zahnrädern verlängert werden kann usw. und kann auch zur Reparatur von Maßtoleranzen verschlissener Teile verwendet werden.Die Dicke der Hartverchromung beträgt im Allgemeinen 5–50 μm.Sie kann auch je nach Bedarf bestimmt werden, teilweise bis zu 200–800 μM. Bei der Hartverchromung von Stahlteilen ist keine Zwischenbeschichtung erforderlich.Bei besonderen Anforderungen an die Korrosionsbeständigkeit können auch unterschiedliche Zwischenbeschichtungen eingesetzt werden.
3. Die milchig weiße Verchromungsschicht ist milchig weiß, mit geringem Glanz, guter Zähigkeit, geringer Porosität und weicher Farbe.Seine Härte ist geringer als die von Hartchrom und Dekorchrom, weist jedoch eine hohe Korrosionsbeständigkeit auf und wird daher häufig in Messwerkzeugen und Instrumententafeln verwendet.Zur Verbesserung der Härte kann auf die Oberfläche der milchig-weißen Beschichtung eine Schicht aus Hartchrom, auch Doppelschicht-Chrombeschichtung genannt, aufgetragen werden, die die Eigenschaften der milchig-weißen Chrombeschichtung und der Hartchrombeschichtung vereint.Es wird häufig zur Beschichtung von Teilen verwendet, die sowohl Verschleißfestigkeit als auch Korrosionsbeständigkeit erfordern.
4. Die poröse Verchromung (poröses Chrom) nutzt die Eigenschaften feiner Risse in der Chromschicht selbst.Nach der Hartverchromung wird eine mechanische, chemische oder elektrochemische Porositätsbehandlung durchgeführt, um das Rissnetzwerk weiter zu vertiefen und zu verbreitern.Die Oberfläche der Chromschicht ist mit breiten Rillen bedeckt, die nicht nur die Eigenschaften von verschleißfestem Chrom aufweisen, sondern auch Schmiermedien effektiv speichern, ungeschmierten Betrieb verhindern und die Reibung und Verschleißfestigkeit der Werkstückoberfläche verbessern.Es wird häufig zum Beschichten der Oberfläche von Gleitreibungsteilen unter hohem Druck verwendet, wie z. B. der Innenkammer des Zylinderlaufs, des Kolbenrings usw. von Verbrennungsmotoren.
⑤ Die Beschichtung mit schwarzem Chrom hat einen gleichmäßigen Glanz, eine gute Dekoration und eine gute Auslöschung.Die Härte ist relativ hoch (130-350HV) und die Verschleißfestigkeit ist 2-3 mal höher als die von Glanznickel bei gleicher Dicke;Seine Korrosionsbeständigkeit ist die gleiche wie bei einer gewöhnlichen Verchromung und hängt hauptsächlich von der Dicke der Zwischenschicht ab.Gute Hitzebeständigkeit, keine Verfärbung unter 300 °C.Die schwarze Chromschicht kann direkt auf die Oberfläche von Eisen, Kupfer, Nickel und Edelstahl aufgetragen werden.Um die Korrosionsbeständigkeit und den dekorativen Effekt zu verbessern, kann als untere Schicht auch Kupfer, Nickel oder eine Kupfer-Zinn-Legierung verwendet und auf der Oberfläche eine schwarze Chrombeschichtung aufgebracht werden.Eine schwarze Chrombeschichtung wird üblicherweise zum Schutz und zur Dekoration von Teilen von Luftfahrtinstrumenten und optischen Instrumenten, Solarenergieabsorptionsplatten und Dingen des täglichen Bedarfs verwendet
Zeitpunkt der Veröffentlichung: 02.07.2023